CASOS DE SUCESSO – NESTLÉ PURINA
Inovação tecnológica para sistemas Batch conforme a norma S88
“A principal exigência da Nestlé Purina para automação de sua unidade na Venezuela foi a utilização à risca da norma S88. A solução encontrada: RSBizWare Batch”
Atentos aos benefícios trazidos pela utilização da norma ANSI/ISA-S88, a Nestlé Purina buscou uma solução que permitisse a redução de custos na automação de seu processo batch na unidade produtora de alimentos para animais de Turmero, Venezuela e que viabilizasse a criação de uma estrutura sólida para utilização em outras companhias do grupo.
Ao fazer a decisão pesou a experiência e a sólida relação de parceria mundial existente entre Nestlé e Rockwell Automation no fornecimento de produtos, serviços e assistência técnica, além da experiência da Techplus Automação, solution provider Rockwell, no desenvolvimento de soluções Batch para indústrias alimentícias.
O desafio foi o pioneirismo na utilização da solução RSBizWare Batch na América Latina, que foi minimizado pelo esforço conjunto da Techplus e Rockwell Automation do Brasil.
O objetivo para desenvolver sua estratégia de automação da manufatura baseado na norma ANSI/ISA-S88 é reduzir o ciclo de desenvolvimento da aplicação, a partir de uma estrutura robusta e padronizada que garanta o aumento de produtividade, flexibilidade e escalabilidade da planta maximizando a utilização dos recursos disponíveis sem comprometer a qualidade e rastreabilidade de seus produtos. A utilização da norma garante o cumprimento de todas exigências e garantiu o retorno sobre investimento da automação em um tempo menor que o esperado.
Preocupada também em posicionar o chão-de-fábrica como parte integrante e ferramenta competitiva para sua base de negócios em uma estratégia colaborativa, outro ponto exigido pela empresa era uma solução de mercado que não fosse dependente de produtos e serviços exclusivos do fornecedor, ou seja pudesse ser integrável por softwares terceiros. O RSBatch atinge todas essas necessidades.
A arquitetura utilizada foi o CLP SLC-552 em rede ethernet.TCP/IP com o supervisório e para I/O distribuído foi utilizado a rede DeviceNet. O software HMI utilizado foi o RSView32, por sua arquitetura distribuída que aumenta sua escalabilidade o RsBatch foi instalado em um servidor específico e standalone onde além do software servidor do batch também centraliza em um banco de dados MS-SQL 7.0 todas as informações da automação.
Evitando um tempo maior de aprendizagem do produto e facilitando o manuseio da aplicação pelos operadores a interface do RSBatch foi implementada diretamente no software MES através de controles ActiveX e pela API disponível com o produto, sem a perda de qualquer funcionalidade e uso de código proprietário. Desta forma a aplicação ficou totalmente integrada. A redução do número de ambientes envolvidos garantiu a potencialização dos recursos disponíveis permitindo a inclusão de funcionalidades como planejamento e controle de produção, controle de estoque de matérias-primas, gerenciamento dinâmico de silos, rastreabilidade de lotes dentre outras. Embora a Rockwell também possua soluções que abrangem esta área como o “Material Track” e o “Batch Campaign”.
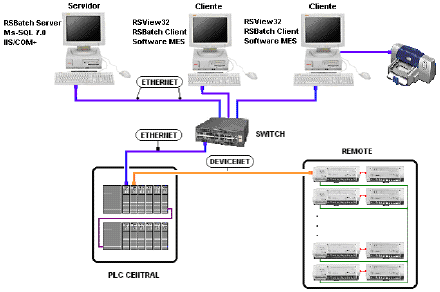
Do ponto de vista da padronização o RSBatch segue rigorosamente as definições da norma e disponibiliza um padrão para desenvolvimento do código e utilização dos endereços no CLP através da PLI (Program Logic Interface). Esta abordagem garante um fácil entendimento por todos envolvidos no projeto e principalmente para manutenção futura. Com sua característica bem estruturada a PLI aumenta muito a engenharia de software do projeto e reduz o custo total de propriedade permitindo que novos equipamentos, fases de operação, e ampliações sejam incorporados ao sistema sem necessidade de redefinição de todos projeto e alteração do código existente. Os equipamentos e fases podem ser testados de modos isolados o que garantem o funcionamento independente, porém integrado cabendo apenas ao Batch Server gerenciar a utilização dos recursos inclusive quando compartilhados por outras unidades (“arbitragem”). Esta interoperabilidade garante a otimização na utilização dos equipamentos com segurança e reduziram drasticamente o tempo de startup do sistema uma vez que os “erros estão isolados”.A facilidade de manutenção e ampliação futura foi um fator decisivo na escolha do software.
Outra e podemos considerar umas das principais vantagens obtidas é a flexibilidade da planta, alcançada através da interface para desenvolvimento de “receitas” (Batch Recipe Editor). Após a determinação das unidades, equipamentos e módulos de controle da célula de processo o funcionamento de todo o conjunto é especificado através do gerenciador de receitas conforme a especificação da norma. Utilizando a linguagem SFC (Sequential Function Chart) as receitas são criadas e permitem tirar o máximo proveito da planta com a customização dos procedimentos e formas de operação; fases podem ser adicionadas ou retiradas, condições de transição entre operações modificadas conforme a necessidade. A partir do uso de parâmetros dinâmicos permitidos nas receitas foi possível integrar o sistema de gerenciamento de fórmulas do MES a partir da receita mestre, o que otimizou ainda mais o processo de startup de novos batchs quando estes parâmetros não devem ser imputados novamente no sistema e são consistidos automaticamente com a capabilidade dos recursos da planta evitando possibilidades de falhas e interrupções no processo por falta de matéria-prima. A complexidade das receitas e seus detalhes são omitidos do operador que podem agora se concentrar em outras tarefas que garantam a melhoria contínua do processo.
Os resultados e as mudanças drásticas na forma de operação foram perceptíveis rapidamente. Uma grande melhora nos índices de produtividade e qualidade garantiram o aumento da eficiência da planta que em conjunto com as ferramentas de MES permitiram uma manufatura mais enx7uta com inventários mais reduzidos e tempo de processos menores e mais confiáveis. A flexibilidade da planta garantiu à engenharia de produtos e qualidade a redução do tempo de ciclo de desenvolvimento de novos produtos uma vez que alterações podem ser realizadas mais rápidas, durante a produção sem a necessidade de programação de paradas e os resultados refletem as capacidades reais da planta. Itens como estes causaram impactos diretos nos custos e no poder de competitividade da empresa o que garantiu um rápido retorno do investimento do projeto.